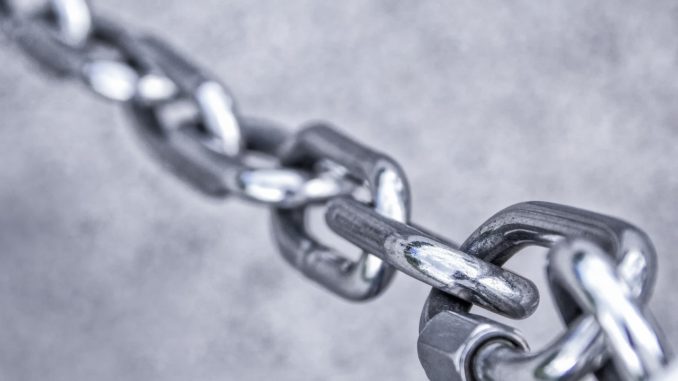
By Sam Rothwell, team lead, HSO
Given the volatile political and economic environment, manufacturers increasingly need to plan for uncertainty and find ways of maximising efficiency in the way they run their operations. One of the biggest areas of concern for many is the supply chain. Manufacturers across multiple sectors of the economy are either planning to, or already stockpiling, in a bid to ensure business as usual.
The fixing and fasteners industry has not been immune from this development. As early as November 2018, Diploma, the FTSE 250 firm which supplies components for Formula 1 cars, said that it had started building inventory levels of parts ahead of the pending Brexit. The firm said it was stockpiling some of its ‘faster-moving product lines’ in the UK. That includes wires and fasteners used by motor and aerospace clients. More recently, Hexstone a leading UK-based supplier of fasteners and fixings, put over £3m extra stocks in place as a contingency for Brexit difficulties in the supply chain.
Today though we are seeing examples of stockpiling in a wide array of different manufacturing sectors across the UK. Indeed, the latest snapshot survey from IHS Markit and the Chartered Institute of Procurement and Supply, indicates that increasing concerns about Brexit disruption resulted in more businesses building up stocks in December 2018.
According to Duncan Brock, group director at the Chartered Institute of Procurement & Supply: “Preparation and mitigation were the key activities in the manufacturing sector this month resulting in a small improvement in overall activity. Businesses stockpiled raw materials and finished goods at near survey-record rates in readiness for possible Brexit-related supply chain disruptions.
“Stockpiling is, however, getting harder as available warehouse space diminishes. Ian Wright, the chief executive of the food and drink federation, recently told MPs that warehouses around the UK for frozen and chilled food are “for all practical purposes booked out at the moment.”
We are certainly seeing growing examples of wholesalers as well as manufacturers themselves stockpiling goods as concerns over the proximity of Brexit start to impact the wider manufacturing supply chain. In summer 2018, the UK government recommended that wholesalers increase their stocks of medicines to ensure patients continue to get access in the event of a ‘no deal Brexit’. Earlier this year, it was reported that wine wholesalers were stockpiling products ahead of Brexit.
Some manufacturers see the current political situation as an area of risk over which they have minimal control. In line with this, a recent survey commissioned by HSO asked decision-makers in the manufacturing industry to name the main risk factors organisations face today in running their supply chains. 39% of respondents referenced ‘risks associated with the broader political or economic environment (including Brexit)’, while just 6% stated ‘there are no main risk factors faced.’
So, beyond stockpiling, what can manufacturers do to reduce the risk posed by political uncertainty to their extended supply chains? For some, especially those in less regulated or globally-integrated industries, the long-term answer might be to bring their supply chain closer to home.
That said, in the current environment, it is critical that manufacturers focus, above all, on best meeting short-term needs. That focus will certainly require enhanced supply chain visibility, especially regarding the location of product components and finished goods.
As they can’t directly influence the supply chain situation at a macro level, manufacturers must instead concentrate on ensuring information flows quickly from the supply chain to manufacturing decision-makers so that they can make fast and accurate ‘flex-plans’ and best optimise operations to deal with challenges arising.
Technology will be crucial in delivering this enhanced visibility and operational flexibility. In line with this, we may see some manufacturers redesigning the supply chain architecture, a process likely to include the implementation and integration of a range of new technologies from data analytics to the Internet of Things to enterprise resource planning (ERP).
ERP can play a key role across this extended supply chain by offering manufacturers the opportunity to reduce overheads and operational costs through automation of workflow, and the flexibility to adapt to meet changing market or customer circumstances or future business growth and expansion. Moreover, there are likely to be fewer IT issues to manage as manufacturers will be operating a more connected and controlled environment.
We are also seeing supplier collaboration portals rise up the agenda. These provide a single shared view of data, enabling manufacturers to collaborate more closely with supply chain partners and resolve problems faster. Together with ERP and general business software, they will be especially important in keeping that crucial conduit of information flowing across the supply chain and providing enhanced supply chain visibility to key supply chain players.
Don’t forget to follow Dealer Support on Twitter!
Be the first to comment